Development of a new technologies of manufacturing of functional materials
Development of a new technologies of manufacturing of functional materials at the Institute of Metallurgy and Materials Science of the Polish Academy of SciencesThere is a long tradition of research on functional materials in the Institute of Metallurgy and Materials Science of the Polish Academy of Sciences. It is related with light alloys, shape memory materials, composites, biomaterials and metallic glasses and nanomaterials. New materials requires new technologies connected with a grain refinement, faster solidification, often evaporation, therefore such technologies have to be applied like powder metallurgy, severe plastic deformation, melt spinning, casting from the semisolid range and others. Concerning shape memory materials in the Institute were cast mainly copper base materials due to real problems with casting of NiTi alloys which are very reactive and in addition very sensitive with transformation temperature to the composition. Fig.1 shows changes of martensitic transformation temperature of CuAlNiTi brasses accompanying grain size changes and the electric switch elaborated in the IMIM PAN using melt spun materials
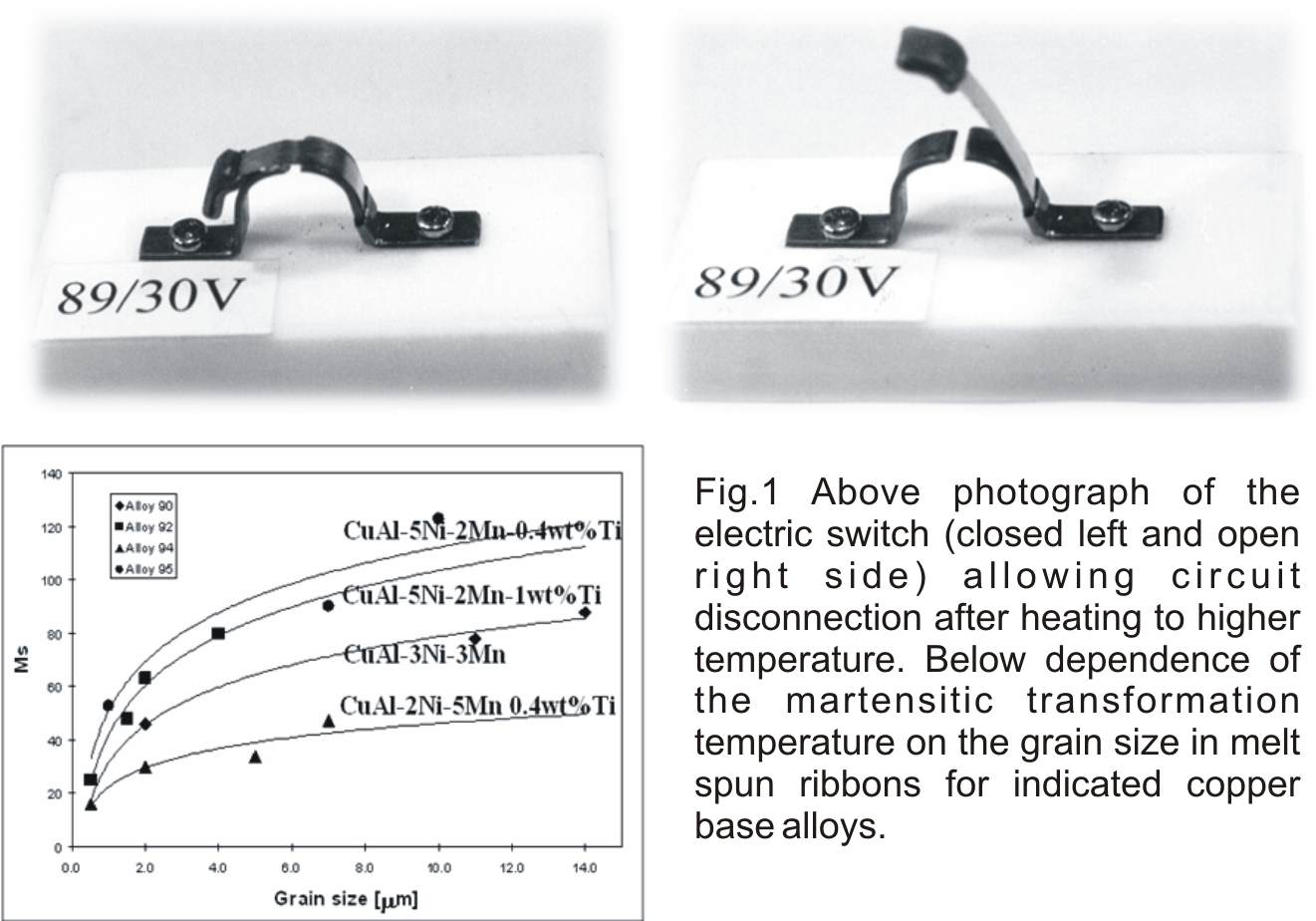
The equipment for melt spinning was developed during years in order to cast ribbons in cleaner atmosphere, containing less oxygen causing degradation of the structure of ribbons. Next micrograph shows the old equipment allowing casting of ribbons only at protective gas flow in not very clean atmosphere, however better than in the air and on the right side and on the right side the new equipment allowing casting of alloys melting up to 1300oC in a clean atmosphere better than 10-3 of gas purity, due to sealed construction and possibility to pump out the air, allowing injecting of a liquid metal on the rotating copper wheel with a linear rate up to 6o m/s.
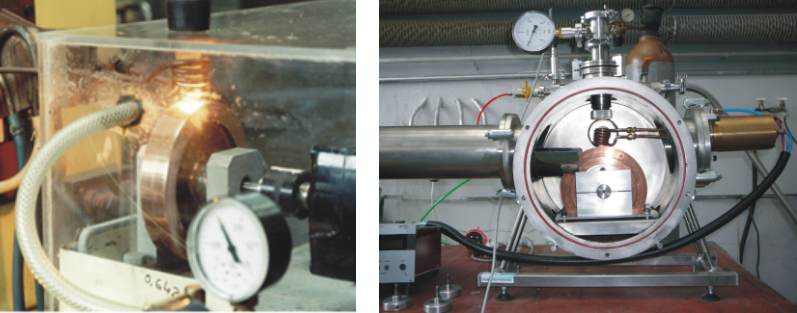
The research on shape memory alloys was also carried out in the direction of training of the NiTi shape memory alloy and the equipment constructed in IMIM by master student Łukasz Rogal was awarded the first prize in the student research wok competition at the Academy of Mining and metallurgy. The constructed equipment is shown in Fig,3a and presently small mount of TiNi alloys can be cast at IMIM PAN due to constructed crucible free casting presented in Fig.5b
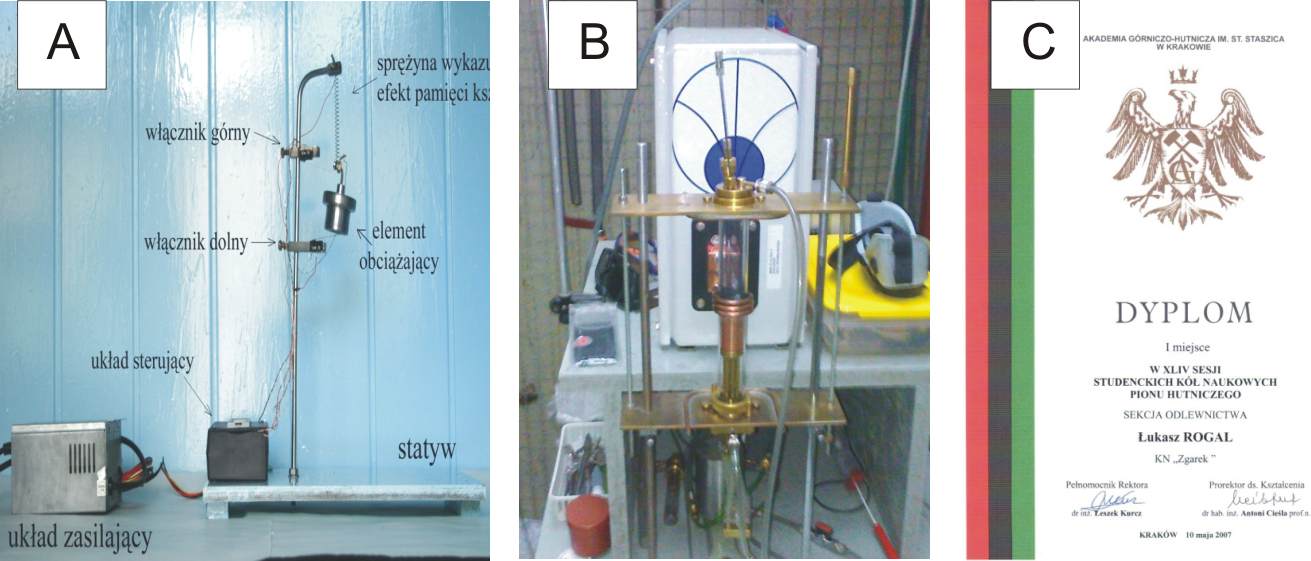
Another direction of materials development in IMIM PAN is powder metallurgy and composite forming starting from ball milled powders. This technique allows to obtain nanocrystalline materials by hot pressing of milled powders Due to high energy milling powders decrease its grain size down to about 30 nm and after hot compaction in spite of sopme grain growth one can obtain bulk nanomaterials. In Fig.4 it is shown how the grain size is refined during milling by multiple hitting and joining of powders particles. The containers containing steel balls and powders in weight relation 10 : 1 are filled in a chamber shown in Fig.5 to avoid presence of the oxygen within containers, which would cause oxidation of powders . Such a technique can also be used and is called reactive milling, however it is not used in IMIM PAN so far.
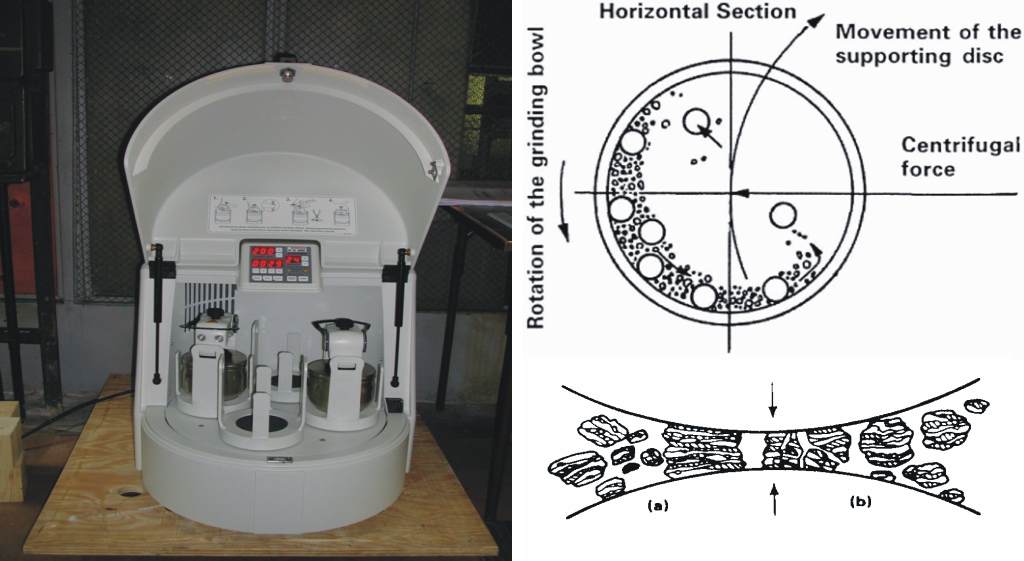
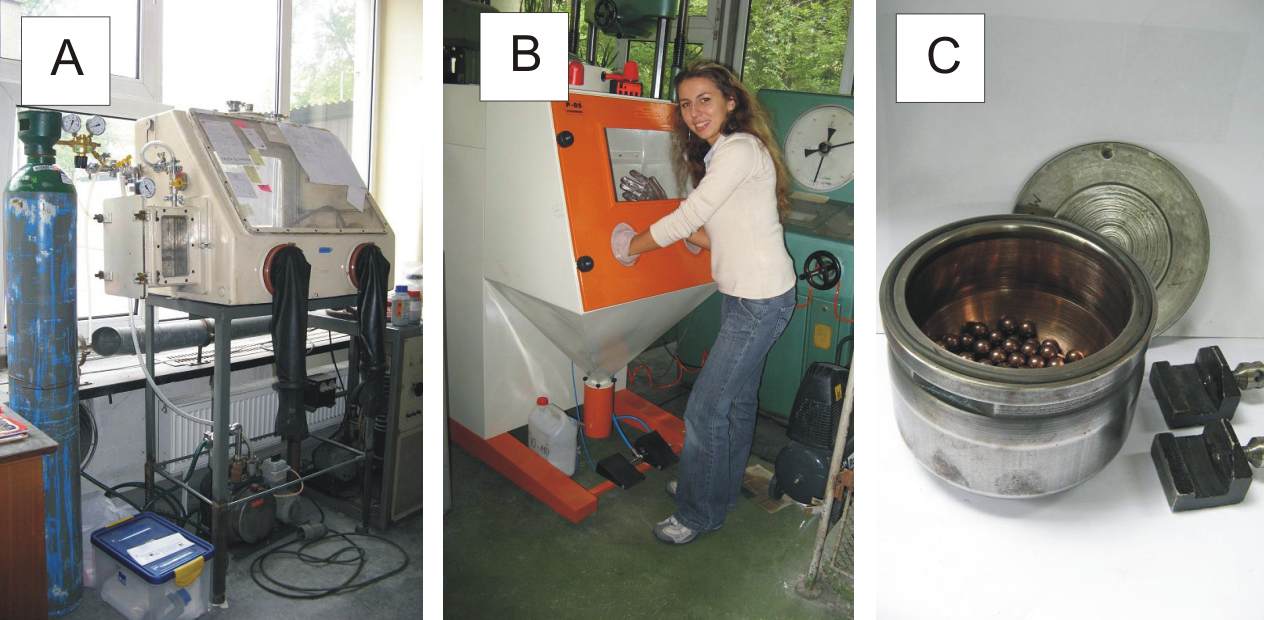
Powders after milling has to be compacted and it is done using specially constructed equipment for uniaxial hot pressing in vacuum presented in Fig.6. The dies for hot compaction made from heat resistant steel are shown in Fig. 6b and hot pressed disc in Fig.6c. Usual temperature of hot pressing was 380oC and pressure 600 MPa.
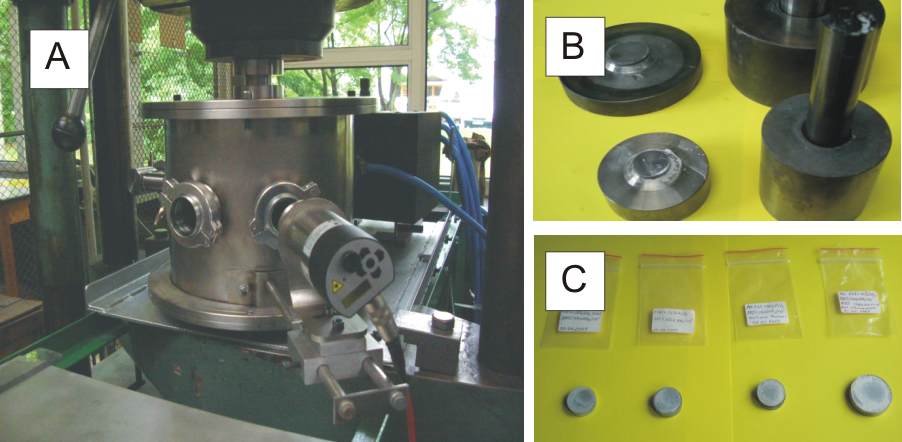
The discs from 7475 nanocrystalline alloy powders obtained by ball milling and nanoceramic ZrO2 poder attain compression strength of 1000 MPa, what is much more than can be obtained for age hardenable aluminum alloys even from 7XXX series. Another technology developed recently at IMIM PAN in the frame of COST 541 European Project is thixoforming of steel. Fig.7 shows the constructed equipment allowing thixoforming of steel from semisolid range at a rate of 2 m/s

The equipment together with measurements of the high temperature thermal properties allowed to obtain thixoformed steel samples from a high carbon tool steels such as M2 or X210CrW12 steel from semisolid range cast at 30-40 % of liquid phase as confirmed by DTA studies. Results were presented on several international conferences and are the subject of PhD thesis. Another equipment developed at IMIM PAN is connected to nanomaterials formation using top down method i.e. by grain refinement of bulk samples The methods used are presented schematically in Fig, 8 and are related to ECAP (Equal Channel Angular Pressing) ARB, (Accumulated Roll Bonding), GB Groove Pressing HPT (High Pressure Torsion).
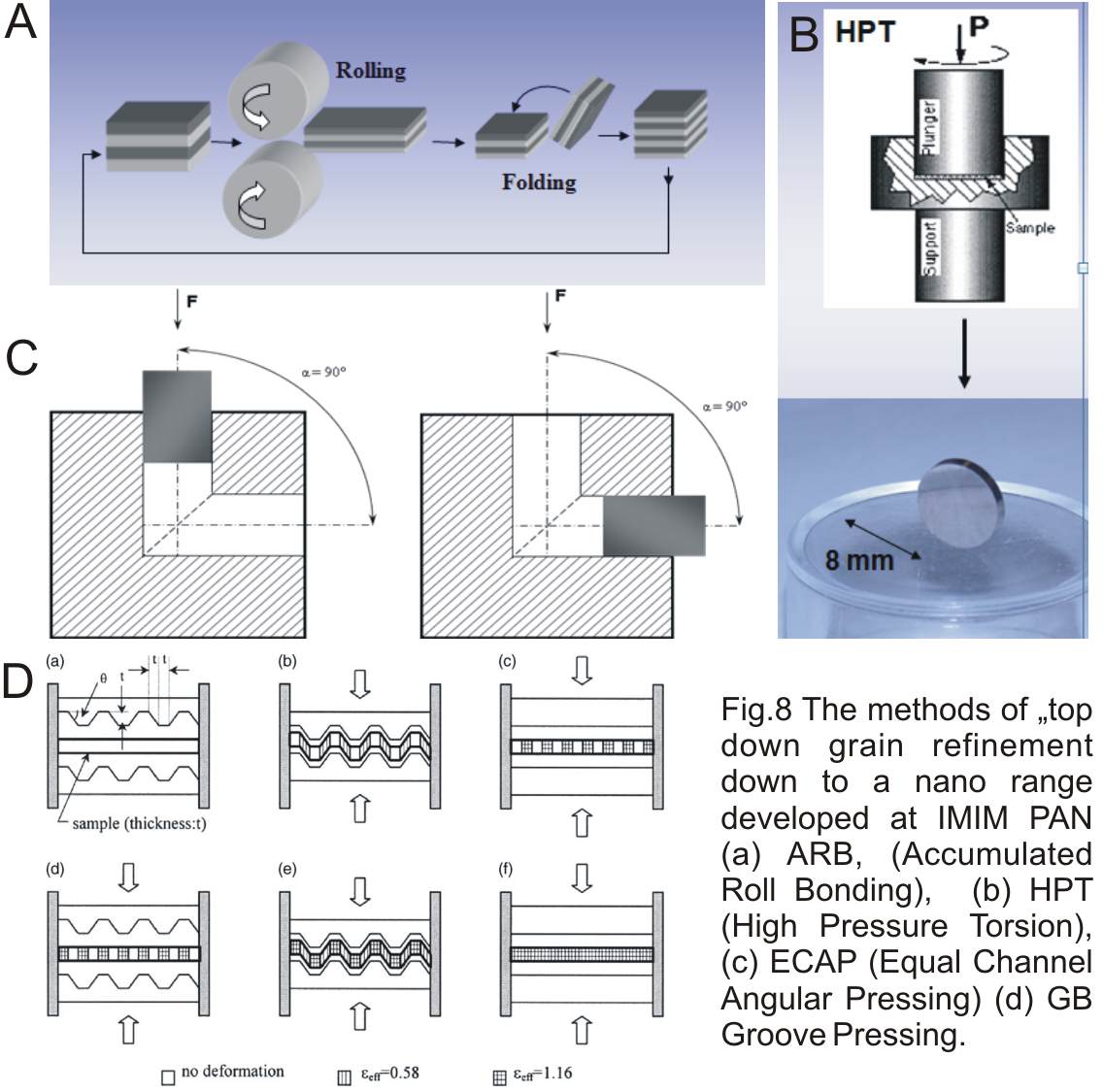
Fig.8 shows four basic ways to refine the grain size with a possibility to a nano range by (a) ARB, (Accumulated Roll Bonding), (b) HPT (High Pressure Torsion), (c) ECAP (Equal Channel Angular Pressing) (d) GB Groove Pressing. All methods are developed at IMIM PAN, ECAM in Laboratories of Plastic Deformation and Functional Materials, ARB at Plastic Deformation Laboratory and groove pressing in the Functional Materials Laboratory. The first three methods were used in recently defended PhD thesis.
Multifunctional materials (pdf file - 1,8MB)
back